Why Frontline Involvement is Essential for Maximizing Equipment Life
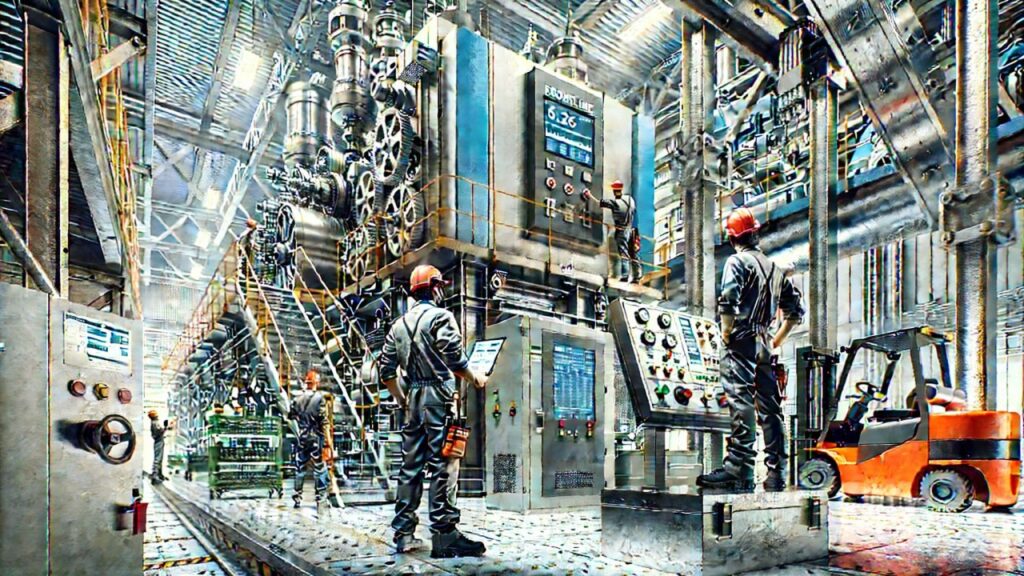
Maximizing the life of your equipment requires more than just a good maintenance plan—it depends on the people who work with the machinery every day.
Your frontline workers are the first to notice when something’s off, and their involvement in the maintenance process can be the key to extending equipment life and preventing costly breakdowns.
Here’s why involving your frontline team is crucial for getting the most out of your assets.
1. Early Detection of Issues
Your frontline team spends more time with your equipment than anyone else. They can detect small issues before they escalate into major problems—things like unusual sounds, vibrations, or performance changes. By encouraging workers to report these early warning signs, you can address potential issues before they lead to expensive breakdowns or extensive repairs.
Training your team to recognize these signs and empowering them to act quickly is one of the most effective ways to prevent minor problems from becoming major ones.
2. Real-Time Feedback Improves Maintenance Schedules
Frontline workers provide real-time, on-the-ground insights into how your equipment is performing. Their feedback is invaluable for adjusting maintenance schedules to meet actual equipment needs. If your team reports that certain machines are showing wear sooner than expected, it may be time to adjust your maintenance intervals.
By involving your workers in the scheduling process, you can fine-tune your preventative maintenance programs, ensuring that your equipment gets the care it needs at the right time.
3. Enhancing Equipment Knowledge
Frontline involvement also helps build a deeper understanding of the equipment. When workers are actively engaged in maintenance efforts, they become more familiar with the ins and outs of each machine. This leads to more informed decision-making and faster responses when issues arise.
The better your team knows the equipment, the more proactive they can be in maintaining it, which ultimately leads to longer equipment life and fewer breakdowns.
4. Creating a Culture of Accountability
When your frontline workers are involved in maintenance, they take ownership of the equipment’s performance. This sense of accountability leads to greater care in how they operate and maintain machinery. It also fosters a collaborative environment where everyone is responsible for extending equipment life, rather than leaving it solely to the maintenance team.
This culture shift can have a profound impact on the longevity and performance of your equipment, reducing the risk of human error and encouraging best practices across the board.
5. Improving Maintenance Accuracy
Workers who interact with equipment daily can spot inconsistencies that might not be visible to a technician doing periodic checks. Whether it’s recognizing an unusual part failure or knowing when a machine’s performance is declining, their insights are critical for accurate maintenance planning.
By integrating frontline feedback into your maintenance strategy, you can ensure that your maintenance efforts are more targeted and efficient, further enhancing the lifespan of your equipment.
The Power of Frontline Involvement
Involving your frontline team in the maintenance process isn’t just a best practice—it’s a crucial element of maximizing equipment life. Their early detection of issues, real-time feedback, and deep knowledge of machinery can make the difference between a well-maintained asset and an unexpected breakdown.
By fostering a culture of accountability and collaboration, you can extend the life of your equipment, improve reliability, and keep your operations running smoothly.
Want to learn more about integrating frontline workers into your maintenance strategy? Contact AMSS Advanced Management Systems & Services, Inc. today to find out how we can help you implement strategies that maximize equipment life and boost reliability.