Building a Maintenance Plan that Aligns with Your Plant’s Operational Goals
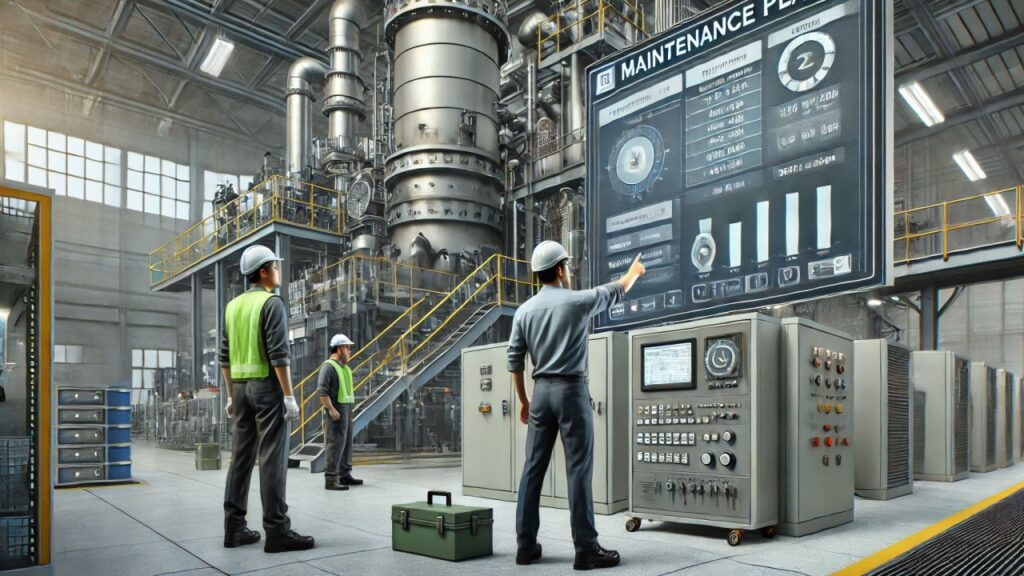
A well-executed maintenance plan does more than just keep equipment running—it supports your entire plant’s operational goals.
Aligning your maintenance strategy with business objectives can boost productivity, reduce costs, and enhance overall efficiency.
Here’s how to create a maintenance plan that drives success across your plant.
1. Understand Your Plant’s Key Objectives
Before designing your maintenance plan, it’s crucial to understand your plant’s broader operational goals. Are you focused on maximizing output, improving quality, or minimizing operational costs? Knowing these priorities will help you tailor a maintenance strategy that aligns with these objectives.
For example, if increasing production output is a key goal, prioritize maintenance activities that reduce downtime and enhance equipment reliability.
2. Assess Current Maintenance Processes
Take a close look at your existing maintenance practices. Are they contributing to or hindering your plant’s operational goals? An honest assessment can reveal inefficiencies, such as excessive reactive maintenance or poor scheduling, that may be holding back your progress.
A gap analysis can help identify areas for improvement and ensure that your maintenance plan supports, rather than disrupts, your plant’s operations.
3. Integrate Proactive Maintenance Strategies
Reactive maintenance often results in unplanned downtime, which can derail operational goals. To align with your plant’s objectives, incorporate proactive maintenance strategies like preventative and predictive maintenance.
Proactive maintenance minimizes unexpected breakdowns, keeps equipment running smoothly, and helps your plant maintain steady productivity levels. Using technologies such as IoT sensors and CMMS software can further streamline these processes and align them with your operational needs.
4. Prioritize Critical Equipment
Not all equipment contributes equally to your plant’s goals. Identify which machinery is most critical to your operations and prioritize maintenance efforts accordingly. This targeted approach ensures that key equipment stays operational, directly supporting your plant’s productivity and output targets.
Developing an equipment criticality ranking can guide maintenance scheduling and resource allocation, making your plan more efficient and aligned with your plant’s needs.
5. Train Your Team on the Plan’s Objectives
A maintenance plan is only as good as the team that executes it. Ensure that your maintenance staff understands how their work contributes to the plant’s larger goals. Training sessions that connect day-to-day maintenance activities to overall plant objectives can boost motivation and effectiveness.
Regular team briefings and workshops can help keep everyone on the same page and reinforce the importance of aligning maintenance efforts with the plant’s mission.
6. Measure and Adjust Your Plan
Building an effective maintenance plan isn’t a one-time task—it requires continuous improvement. Regularly review KPIs such as equipment uptime, Mean Time Between Failures (MTBF), and Mean Time to Repair (MTTR) to assess the plan’s effectiveness.
Adjust the plan as necessary to respond to changes in operational goals, production demands, or new equipment. This ensures that your maintenance strategy remains aligned with your plant’s evolving needs.
Aligning Maintenance with Operational Success
A maintenance plan that aligns with your plant’s operational goals is essential for achieving long-term success.
By understanding your plant’s objectives, prioritizing critical equipment, and incorporating proactive strategies, you can build a maintenance plan that supports productivity and efficiency.
Looking to develop a maintenance plan that drives your plant’s success? Contact AMSS Consulting for a consultation on aligning maintenance strategies with operational goals.