Reactive Maintenance Is Costing You—Here’s How to Fix It
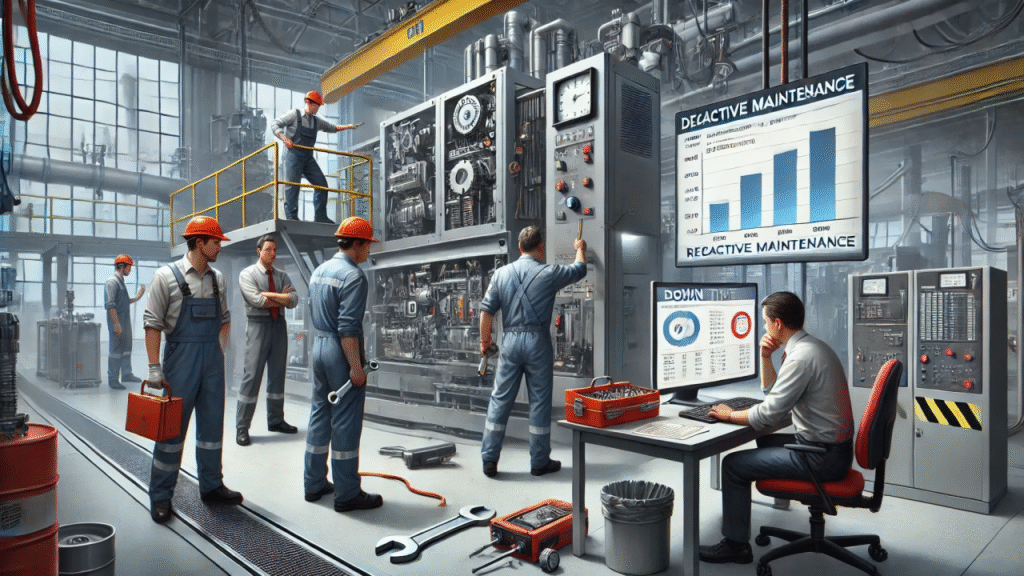
If your team is constantly fixing equipment after it breaks, you’re stuck in a reactive maintenance cycle—and it’s draining your budget.
Emergency repairs, unplanned downtime, and expedited parts add up fast.
Here’s how to move from reactive to proactive maintenance and cut costs while improving reliability.
The High Cost of Reactive Maintenance
- Unplanned Downtime – Production losses and missed deadlines.
- Higher Repair Costs – Emergency labor and rush shipping for parts.
- Shorter Equipment Life – Frequent breakdowns lead to premature replacements.
How to Shift to Proactive Maintenance
- Condition-Based Maintenance (CBM) – Monitor key metrics like vibration and temperature to detect early warning signs.
- Predictive Maintenance (PdM) – Use IoT sensors and historical data to predict failures before they happen.
- Planned Preventative Maintenance (PM) – Schedule maintenance at optimal intervals to keep equipment running longer.
The Bottom Line
Proactive maintenance lowers repair costs, prevents downtime, and extends equipment life. If you’re tired of chasing breakdowns, it’s time to make a change.
Want a strategy to break the reactive cycle? Contact AMSS Consulting today and let’s build a smarter maintenance plan.