Your Failure History Is More Valuable Than You Think
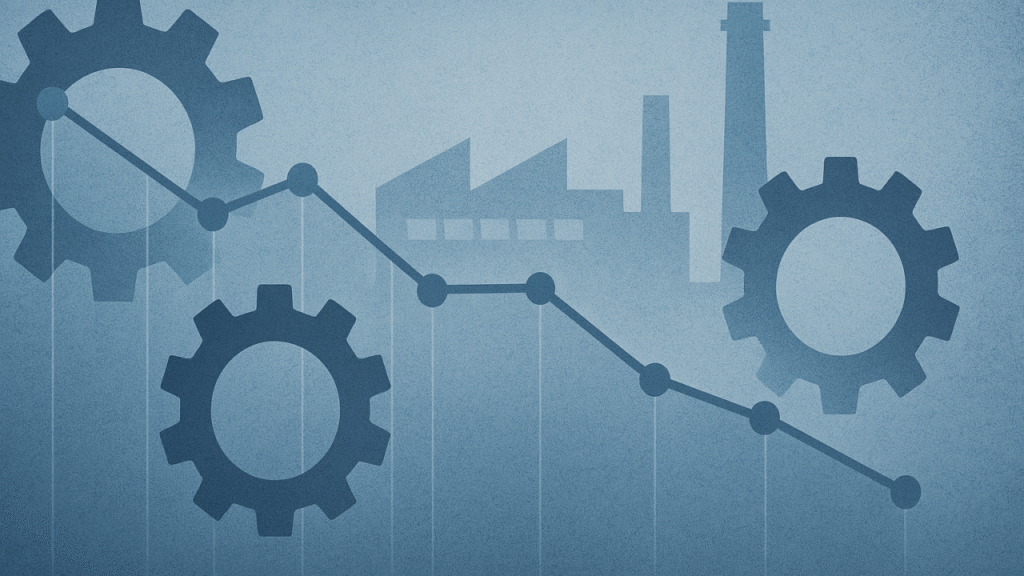
Every breakdown tells a story. But if you’re not capturing and reviewing failure data, you’re missing out on insights that could save you time, money, and headaches.
The best maintenance teams use failure history to:
- Adjust PM schedules
- Stock the right parts
- Improve training
- Even guide future equipment purchases
Here’s how to make failure history a core part of your decision-making process:
1. Start with Clean, Consistent Data
It starts with logging failures properly in your CMMS. That means:
- Using simple, structured failure codes
- Capturing root causes (not just symptoms)
- Logging what was replaced, why, and how long it took
Without good data, your trends will always be fuzzy.
2. Use Patterns to Guide Preventative Maintenance
Are you over-servicing equipment that rarely fails? Or under-maintaining assets with a short MTBF?
Failure history helps you spot which PMs need more attention—and which ones need to be scaled back.
3. Stock Parts Based on Real Usage
Stop guessing what should be on the shelf.
Failure history shows which parts fail the most, how often, and how long replacements typically take. That insight can dramatically improve spare parts planning and reduce downtime.
4. Train Based on Real Gaps
Do certain failure types keep recurring? Are fixes taking longer than they should?
Use that info to tailor training—whether it’s better troubleshooting, faster repairs, or improved PM execution.
5. Make Smarter Capital Decisions
Is one asset eating up a disproportionate share of labor and parts?
Your failure data can make a strong case for replacement—or at least re-engineering.
Bottom line: Past failures should drive future decisions. If you’re not using this data, you’re leaving easy wins on the table.
Want help setting up failure tracking that’s simple, scalable, and effective?
Reply to this email and let’s set up a time to talk.