The Maintenance Meeting That Can Save Hours of Downtime
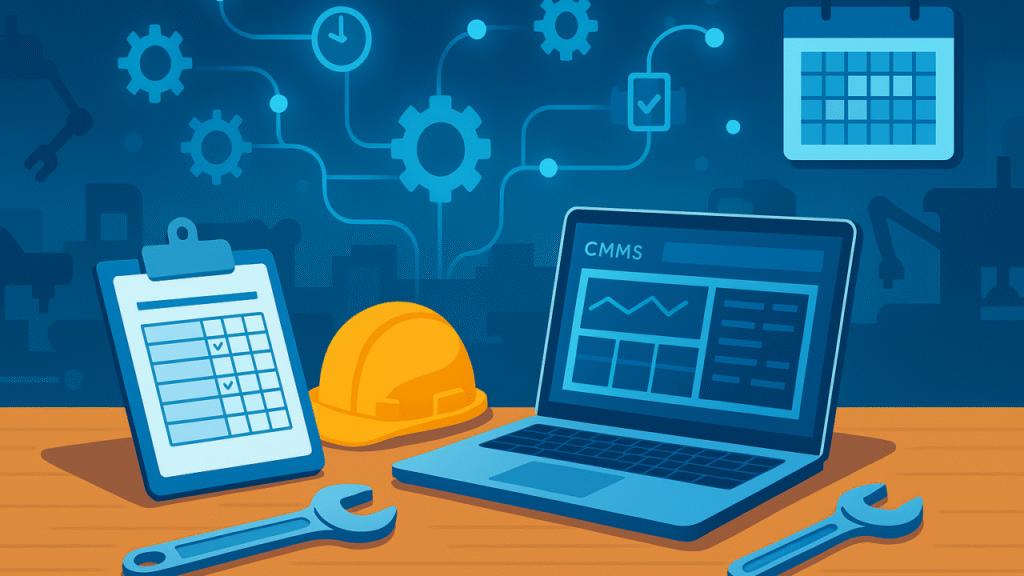
If your maintenance planning meetings feel disorganized—or aren’t happening consistently at all—you’re likely stuck in a reactive cycle that’s costing you time, clarity, and uptime.
But with the right structure, a 30-minute weekly meeting can transform how your team executes maintenance and reduce the firefighting that slows everything down.
Here’s what a world-class planning meeting actually looks like:
Start with the Right People
Keep it lean but cross-functional:
- A planner who owns the schedule and knows the backlog
- A supervisor who understands labor availability and crew capabilities
- A production or operations rep who can confirm access and timing
- (Optional) A reliability or inventory lead for long-lead or high-risk work
Follow a Simple, Consistent Agenda
- Review last week’s plan vs. actual – What got done? What didn’t? Why?
- Check for critical backlog – Are any safety, compliance, or high-impact jobs getting delayed?
- Walk through the coming week – Are the jobs planned, parts available, labor confirmed, and production windows secured?
- Flag high-risk work – Anything that could disrupt production or carry added risk gets called out.
- Adjust and lock the plan – Avoid midweek chaos by finalizing and confirming the schedule.
Stay Focused on Execution
This isn’t a design meeting or a strategy session. Keep it tactical. Use a visual schedule or CMMS dashboard. End every meeting with clear action items and accountability.
Why It Works
When done right, this meeting:
- Keeps priorities aligned between maintenance and operations
- Reduces delays and unplanned work
- Builds discipline around planning and execution
- Frees up hours of wasted labor and equipment downtime each week
If your meetings aren’t delivering results—or they’re not happening at all—it’s likely not a people problem. It’s a structure problem.
Want help setting up a planning process that actually works?
Let’s talk through how to get started.