Train Your Frontline Team to Catch Failures Before They Happen
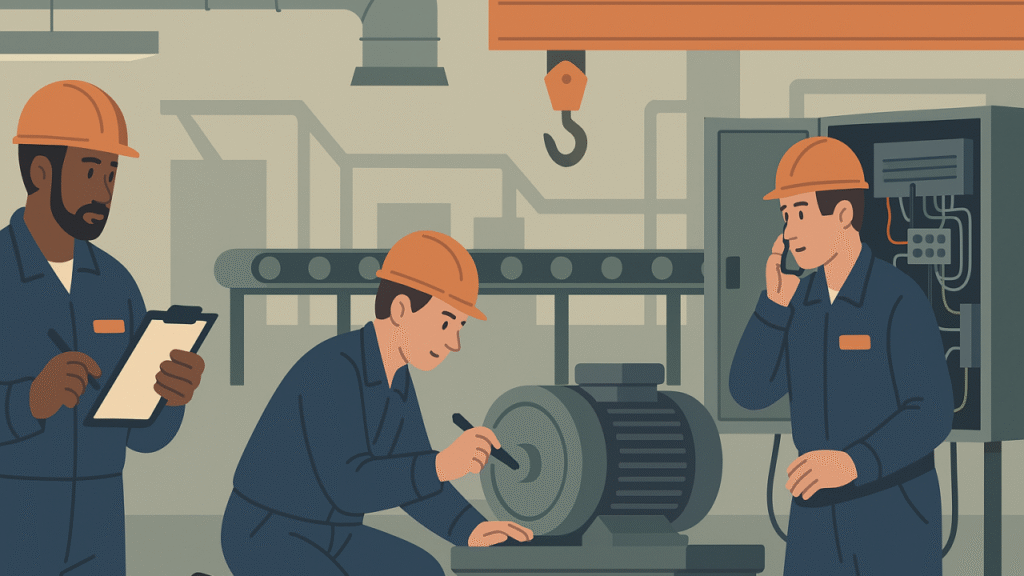
Frontline workers are your first line of defense when it comes to equipment reliability. They see the machines every day—and often spot problems before the maintenance team gets involved.
But without the right training, those early warning signs get missed… and minor issues turn into major breakdowns.
Here’s how to change that.
1. Teach Them What to Look For
Most equipment gives subtle signs before it fails:
- Strange noises
- Leaks or drips
- Vibration or heat
- Irregular performance
Train your team to recognize and report these symptoms. Create a simple checklist they can use during regular operation.
2. Make Reporting Fast and Easy
If it takes too much time or effort to report an issue, it won’t get done.
Use your CMMS or a quick digital form to log issues with as little friction as possible.
Better yet—reward proactive reporting so it becomes part of your culture.
3. Build Operator Care Into Daily Routines
Frontline involvement shouldn’t be a “nice to have.”
Make basic inspections part of their daily tasks:
- Check belts, hoses, gauges
- Listen for abnormal sounds
- Log runtime hours
When operators own the health of their equipment, failures go down—and uptime goes up.
4. Close the Feedback Loop
Let your team know when their reports prevented a failure.
That feedback builds trust, reinforces the value of their role, and drives more engagement over time.
Train Today. Prevent Breakdowns Tomorrow.
Your maintenance team can’t be everywhere—but your operators already are.
With the right training and process, your frontline team can help catch issues before they become problems.
Want help building a proactive frontline program?
Reply to this email and let’s talk through what it could look like for your plant.
- « Previous
- 1
- 2
- 3
- Next »