Prevent Breakdowns Before They Happen: The Power of a Proactive Maintenance Strategy
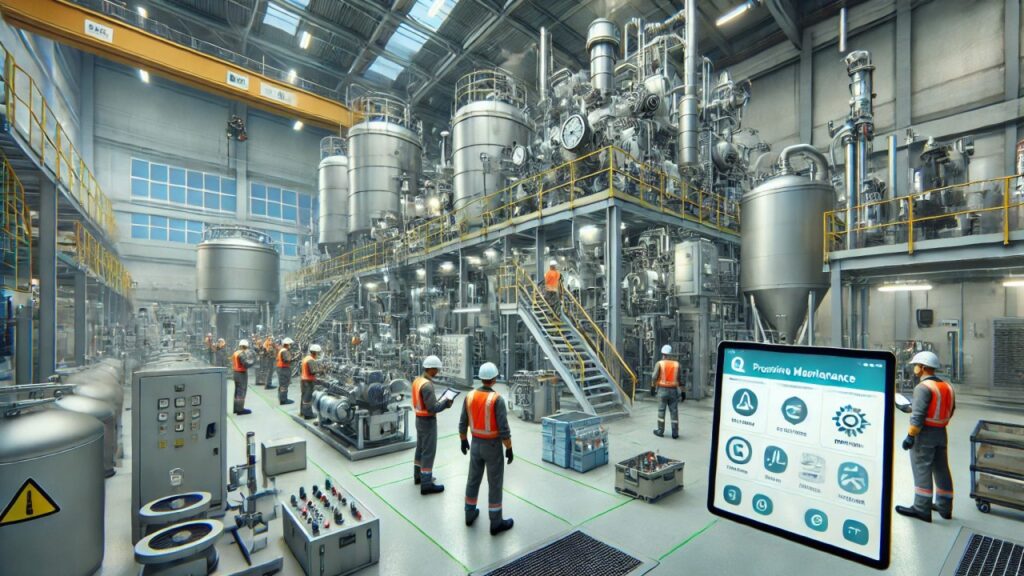
Breakdowns always seem to happen at the worst time, don’t they?
But with a proactive maintenance strategy in place, you can significantly reduce unplanned downtime and keep your operations running smoothly.
By shifting your focus from reactive to proactive maintenance, you’ll extend equipment life, improve reliability, and avoid costly emergency repairs.
Here’s how to get started with a proactive maintenance strategy.
1. Move from Reactive to Proactive
If you’re constantly reacting to equipment failures, you’re stuck in a cycle of emergency repairs and downtime. Proactive maintenance is about staying ahead of issues, identifying potential failures before they occur, and keeping your machinery running at peak efficiency.
This shift not only reduces unexpected breakdowns but also helps you plan and budget more effectively by reducing the need for expensive, last-minute fixes.
2. Leverage Condition-Based Maintenance (CBM)
One of the best ways to stay proactive is to adopt Condition-Based Maintenance (CBM). This strategy monitors real-time data—like temperature, vibration, or pressure—to assess the health of your equipment. Instead of sticking to rigid schedules, maintenance is performed when indicators show that performance is dropping or a failure is imminent.
This approach ensures that maintenance is done when it’s needed, not before or after, saving you both time and money.
3. Incorporate Predictive Maintenance
Take things a step further with Predictive Maintenance, which uses advanced technology like IoT sensors and AI to predict when equipment is likely to fail. By analyzing historical data and current conditions, predictive maintenance helps you forecast issues and schedule maintenance during planned downtime.
Predictive tools provide deeper insights into your equipment’s health, helping you avoid breakdowns and optimize your maintenance resources.
4. Plan Maintenance with Precision
Another key to proactive maintenance is to plan with precision. Instead of generalized schedules, create data-driven maintenance plans that take into account your equipment’s actual performance and wear patterns. Use historical data to determine the optimal maintenance frequency for each machine, reducing both over-maintenance and under-maintenance.
This targeted approach allows you to spend your maintenance budget where it matters most and prevent unnecessary interruptions to production.
5. Engage Your Team in Preventative Efforts
The people who work with the machines day in and day out are often the first to notice when something isn’t quite right. Engage your maintenance team in proactive efforts by encouraging them to report any unusual sounds, vibrations, or performance changes. Their insights can provide early warnings of potential issues.
By fostering a culture of proactive maintenance, you empower your team to help prevent breakdowns before they occur.
The Benefits of Proactive Maintenance
A proactive maintenance strategy doesn’t just reduce unplanned downtime—it improves equipment reliability, reduces repair costs, and helps you better control your maintenance budget. By focusing on Condition-Based and Predictive Maintenance, you can prevent problems before they happen and keep your operations running smoothly.
Ready to prevent breakdowns before they happen? Contact AMSS Advanced Management Systems & Services, Inc. for a free consultation on how we can help you implement a proactive maintenance strategy that works for your business.