Cut Maintenance Costs Without Sacrificing Reliability
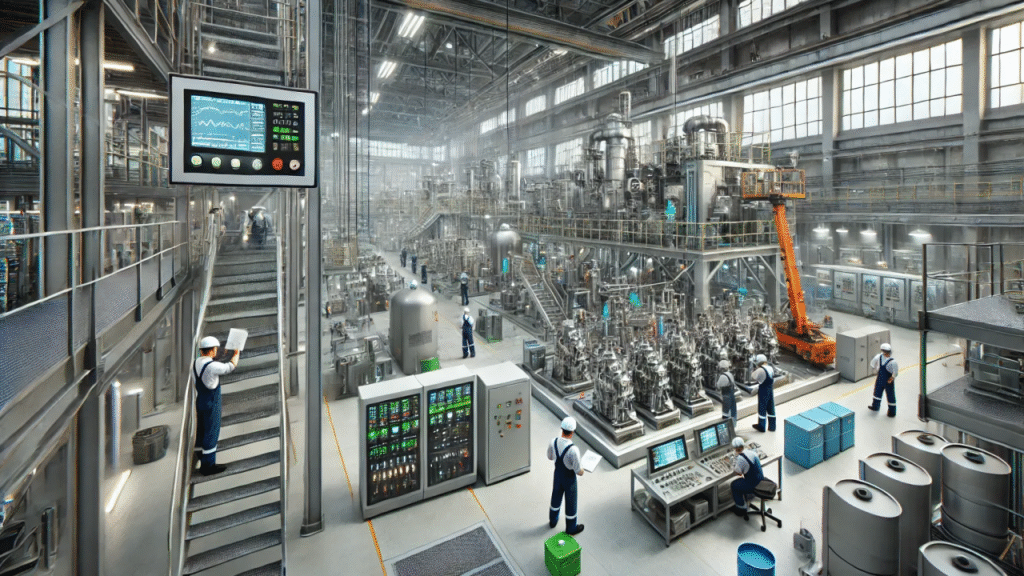
Reducing maintenance costs is a priority for many manufacturing plants, but cutting corners can sometimes compromise the reliability of equipment.
The key is to find strategies that minimize expenses while maintaining peak equipment performance.
At AMSS Consulting, we believe you can achieve both cost reduction and high reliability with the right approach. Here’s how you can get started.
The Importance of Planning and Scheduling
Proper planning and scheduling are essential for reducing maintenance costs. A well-structured maintenance schedule ensures that equipment is serviced at the right time, preventing unnecessary repairs and avoiding costly breakdowns.
By planning ahead, you can minimize the amount of downtime needed for repairs and eliminate inefficient use of labor and contractors. This structured approach ensures that your team spends time where it’s needed most, without over-allocating resources.
Embrace Condition-Based Maintenance (CBM)
One of the most effective ways to reduce maintenance costs without compromising reliability is by implementing Condition-Based Maintenance (CBM). This approach involves monitoring equipment performance in real time and only performing maintenance when specific conditions are met, such as vibration levels or temperature changes.
Condition-Based Maintenance helps you avoid unnecessary maintenance tasks while ensuring equipment is always serviced at the optimal time, extending its life and reducing the need for costly emergency repairs.
Maximize the Value of Your CMMS
A Computerized Maintenance Management System (CMMS) is essential for tracking and analyzing maintenance activities. However, many companies fail to fully utilize the power of their CMMS, leading to missed opportunities for cost savings.
By integrating your CMMS with real-time data and historical trends, you can accurately forecast maintenance needs and avoid reactive repairs. This proactive approach keeps equipment running smoothly while controlling maintenance costs.
Optimize Preventative Maintenance (PM) Programs
Preventative Maintenance (PM) programs are a staple of any maintenance plan, but they can be resource-heavy if not optimized. Regularly reviewing and updating your PM schedule ensures that you’re not over-maintaining equipment or wasting resources on tasks that don’t directly impact reliability.
The key is to focus on the right work at the right time. By aligning your preventative maintenance with actual equipment needs, you can eliminate unnecessary tasks while ensuring your equipment stays reliable.
Leverage Technology and Predictive Tools
With advancements in IoT and AI, companies can now use predictive tools to monitor equipment health and foresee potential failures before they happen. By leveraging these technologies, you can anticipate issues and perform maintenance only when needed, rather than on a fixed schedule.
This predictive maintenance approach not only reduces costs but also improves equipment reliability, as problems are addressed before they result in expensive breakdowns.
Cost Savings Without Cutting Corners
Reducing maintenance costs doesn’t have to mean sacrificing reliability. By focusing on proactive strategies, such as planning and scheduling, condition-based maintenance, and leveraging technology, you can achieve significant cost savings while keeping your equipment running at peak performance.
Ready to lower your maintenance costs without compromising reliability? Contact AMSS Consulting for a free strategy session today and start optimizing your maintenance strategy.
- « Previous
- 1
- 2
- 3
- Next »